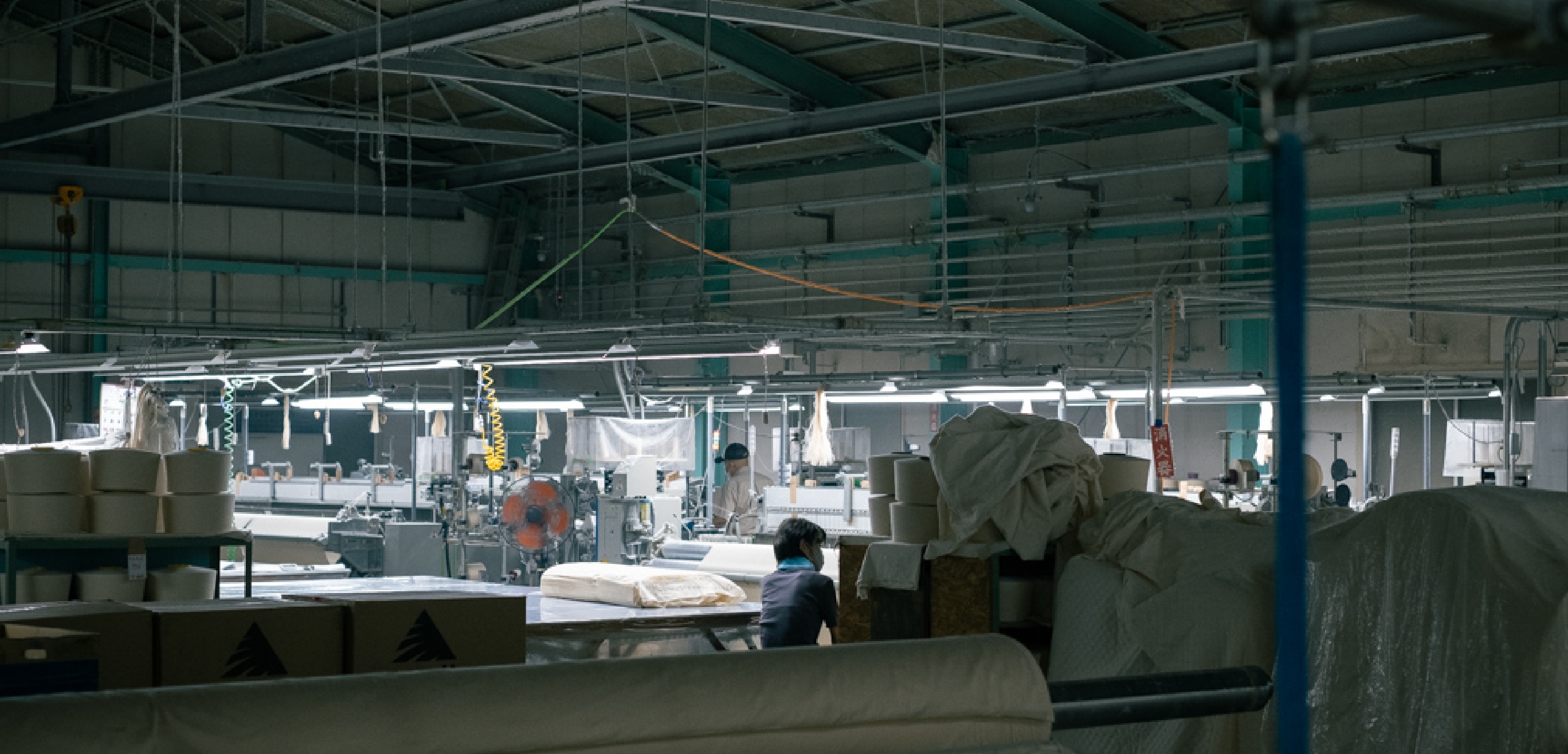
Facilities
The only facilities in Japan,
capable of producing extra-wide (>120 inches in width) and high density (1000TC) bed linens, desired by luxury hotels
Looms
(153 inches wide)
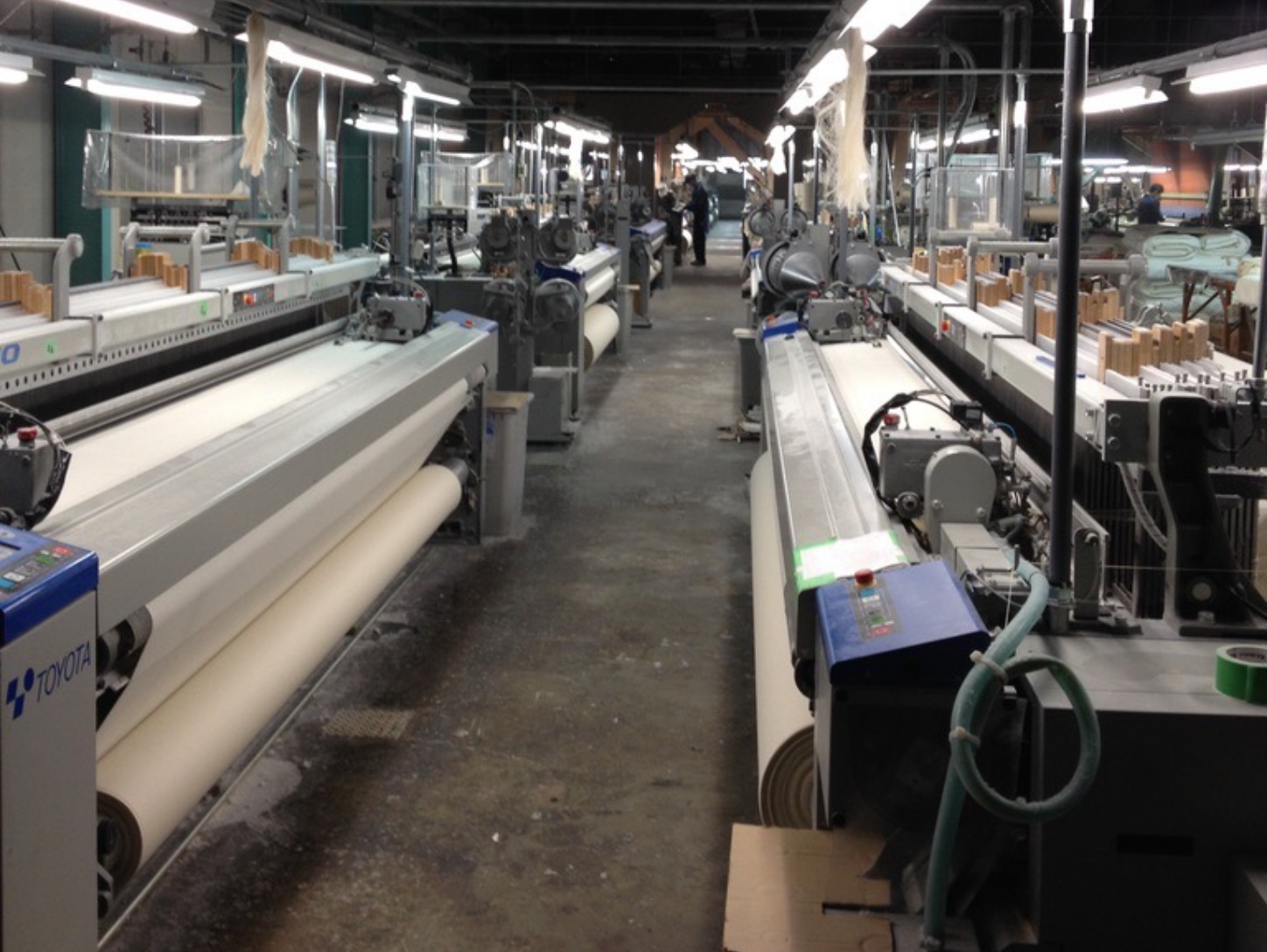
Singeing machine
(157 inches wide)
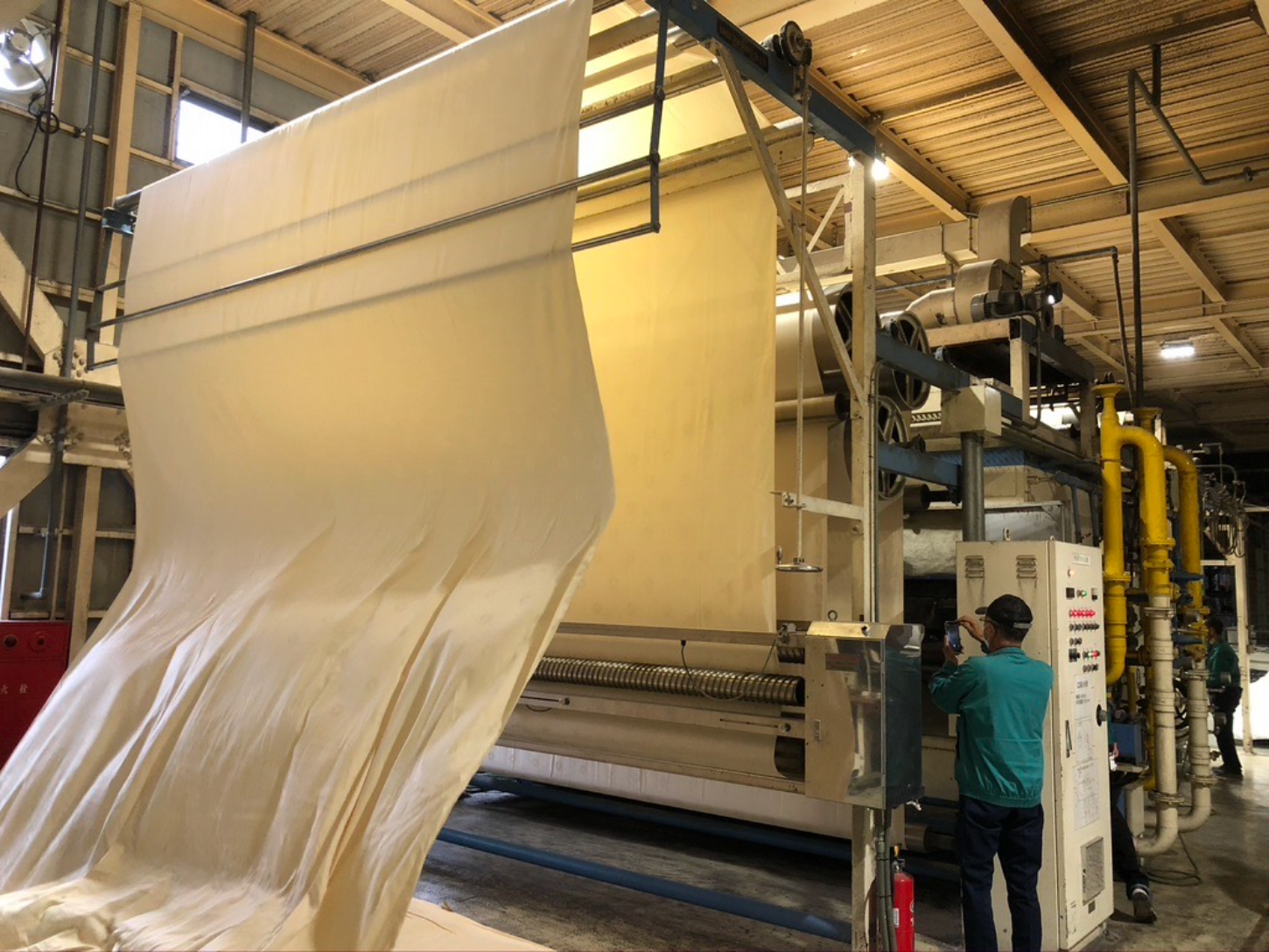
Tenter
(157 inches wide)
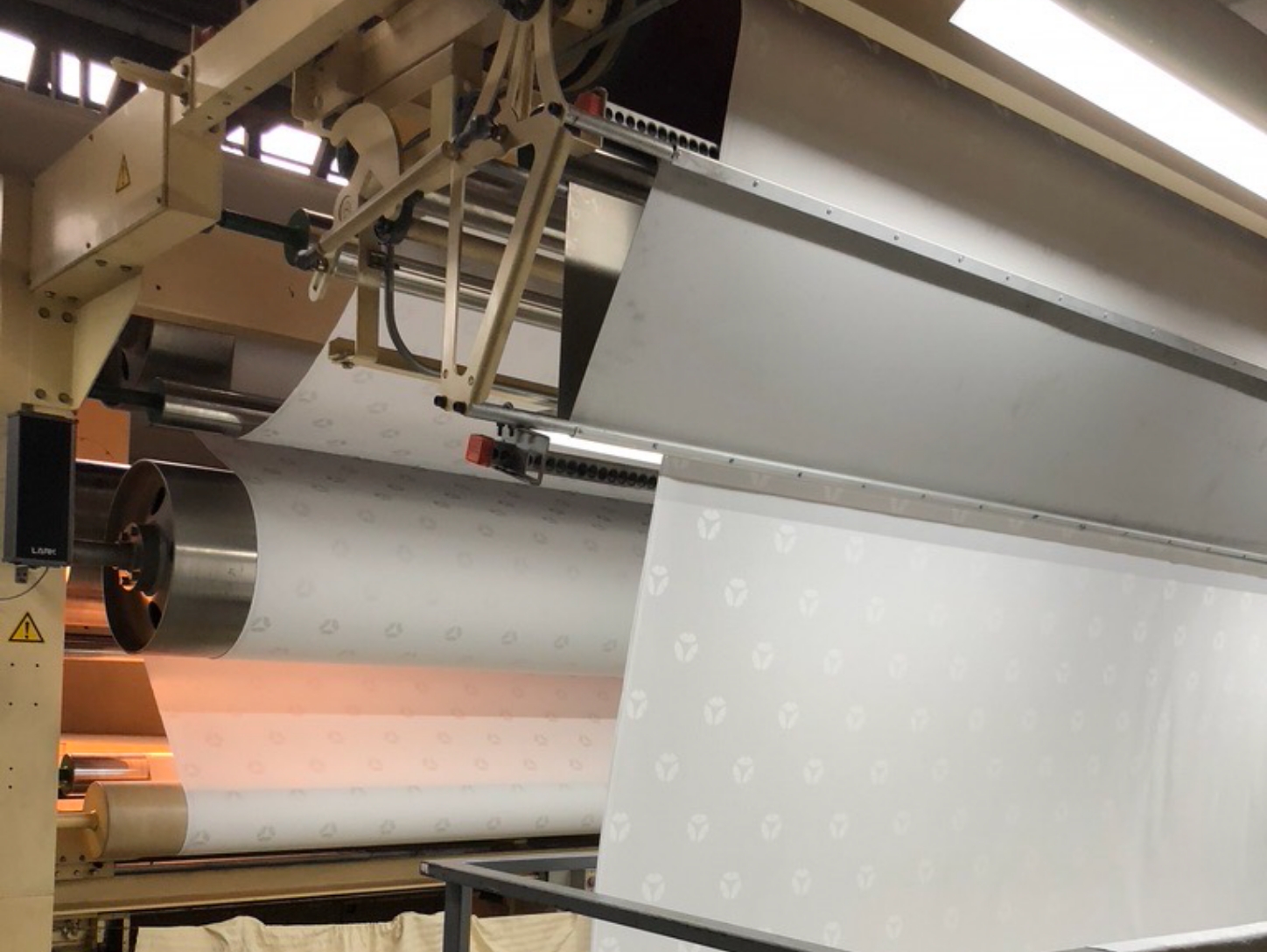
Spreading machine
(157 inches wide)
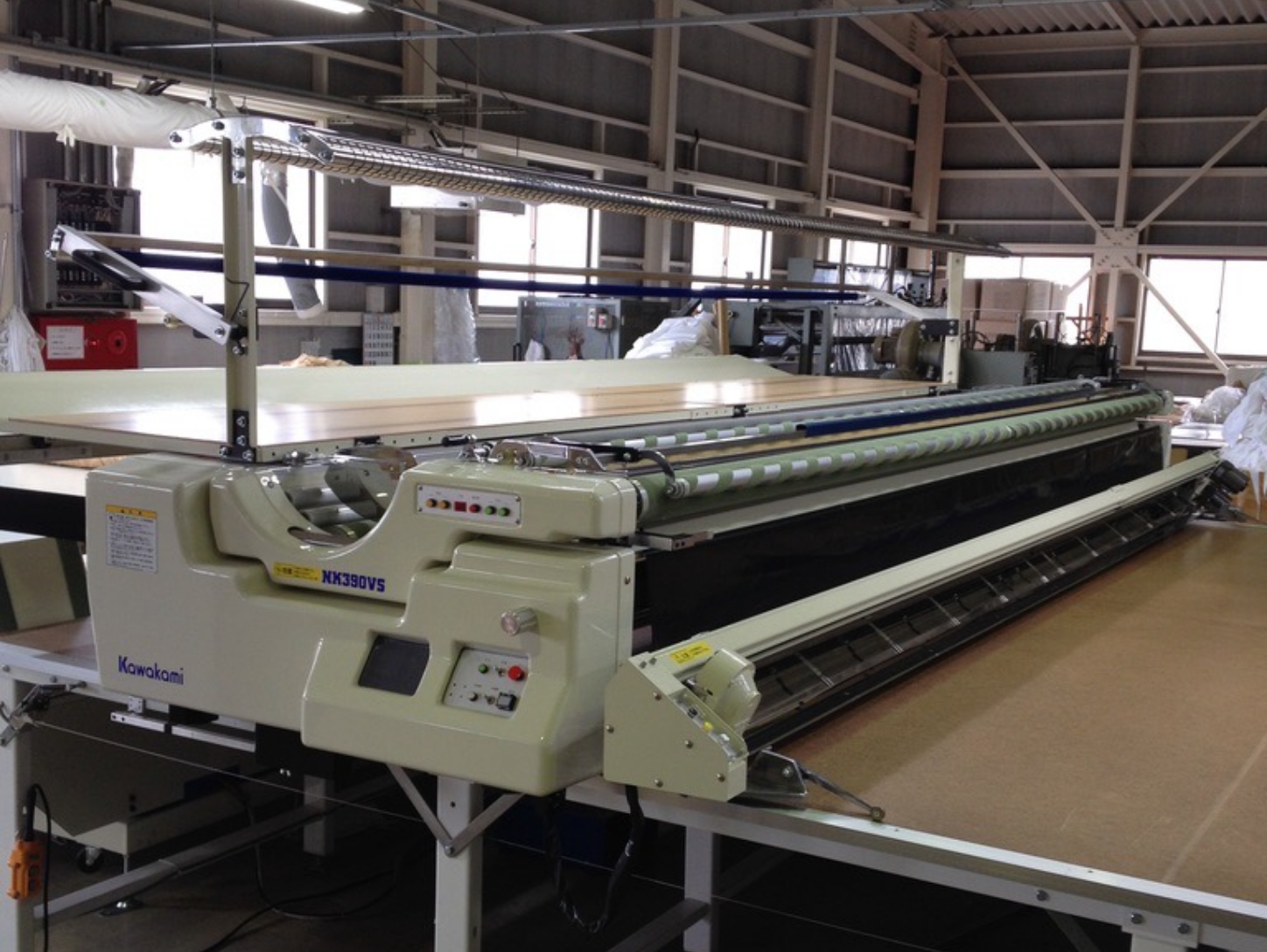
Preparation
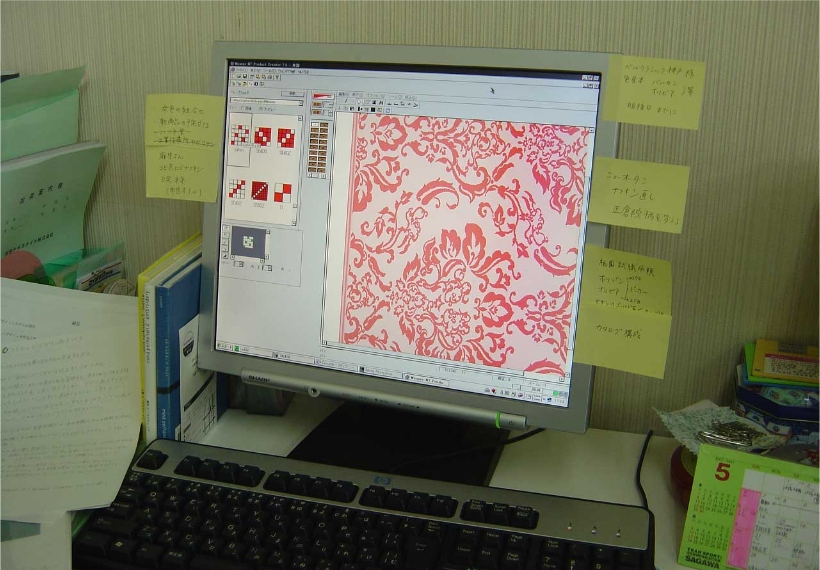
Textile planning and design data creation
Firstly, yarn material, yarn count, yarn density are determined for warp and weft, respectively, to satisfy customer’s desire. Next, fabric construction and woven pattern are determined, and then design is created. Finally, design data are created to be expressible by weaving.
Warping
The warp yarns are arranged in parallel and placed on a warp beam for weaving.
The warping process involves winding the yarn onto the beam, sizing the yarn (to strengthen yarn, if needed), preparing the beam for use on the loom. The photo shows sectional warping, and there are other methods, such as direct warping and beam to beam sizing.
Weaving
Weaving
Our weaving factory is equipped with dobby looms and Jacquard looms, which can produce fabrics up to 153 inches wide. One of the Jacquard devices can control all the hooks independently, and a wide variety of complex patterns and designs is attainable for 138 inches wide fabrics.
Singeing
Spun yarn is an assembly of staple fibers, and some of the fibers project outside from the surface of the yarn due to friction in the weaving process. The resulting protruding fibers need to be removed to enhance overall performance of the fabric like smoother texture and better dyeing quality.
The most common method is gas singeing, which burns off the protruding fibers by passing the fabric over a gas flame. Our factory is equipped with a gas singeing machine for 157 inches wide fabric, which is the largest width in Japan.
Processing / Finishing
Scouring, Bleaching, Dyeing
Natural fibers like cotton and flax include impurities like waxes and pectins, which need to be removed to attain homogeneous uptake of chemicals in the following steps.
This scouring step is followed by the bleaching step to decompose inherent dye components.
The fabric after bleaching show slightly yellowish white (off-white) and becomes white (optical white) by treating with an optical brightener.
Dyeing
Color is applicable to the bleached fabric by using proper dyes, depending on the type of the fiber.Natural fibers can be dyed with reactive dyes, VAT dyes (threne dyes), sulfur dyes, naphthol dyes, direct dyes, acid dyes and so on, while synthetic fibers like polyester require different types of dyes, such as disperse dyes, cation dyes and acid dyes.
Finishing
Finishing is a final process in the textile processing sequence to improve hand feeling or to add an extra functionality, such as antibacterial, deodorization, water repellency, shape stability, etc.
During this process, skewing or bowing of the fabric is corrected, which means the weft yarns are set to be orthogonal to the warp yarns.
Inspection
Inspection/Rolling
After the finishing process, the quality of fabric is determined by checking various defects in terms of color, weaving pattern, hand feeling, stain, skewing, bowing and other weaving or processing defects.
Beaker dyeing / Textile testing
Prior to the dyeing process, the dye composition is determined on a lab scale by using the apparatus shown in the photo, which is called beaker dyeing.
The finished fabric is subjected to various tests to evaluate color fastness and physical properties, such as shrinkage, tear strength, tensile strength, slip resistance, pilling resistance, abration resistance.
Sewing
Sewing
The inspected fabrics are cut and subsequently sewn according to customer’s requests on the size and the sewing specifications, such as double fold hem, bias binding, hidden bias binding and ultrasonic cutting.
After inspection and packaging, the sewn products are scanned by a needle detector to ensure safety and then shipped to customers.